在塑料加工、橡胶制造及食品化工等众多工业领域中,双螺杆挤出机作为核心设备,扮演着将原材料转化为具有特定形状和性能产品的关键角色。而其中,它作为直接接触并处理物料的部件,其设计与性能对产品的质量和生产效率有着直接影响。本文旨在深入探讨双螺杆挤出机螺纹套的结构特性、材料选择、加工工艺以及其在实际应用中的表现,为相关领域的技术人员和研究人员提供有价值的参考。
一、结构特性:精密设计与功能实现
双螺杆挤出机螺纹套,通常由多个螺纹元件组合而成,这些元件按照特定的排列顺序装配在芯轴上,形成连续的螺旋通道。它的设计需考虑物料流动的均匀性、剪切力分布、停留时间控制等多个因素,以确保物料在挤出过程中能够充分塑化、混合并达到所需的物理化学性能。每个螺纹元件的形状、尺寸、螺距以及相互之间的组合方式,都是根据具体加工需求精心设计的。例如,某些区域可能采用深槽设计以增加剪切力,促进物料混合;而另一些区域则可能采用浅槽或平滑设计,以减少不必要的热量产生,保护物料特性。
二、材料选择:耐磨与耐高温的双重考验
鉴于它在工作过程中需要承受高温、高压以及高速旋转带来的强烈摩擦,其材料选择至关重要。常见的材料包括硬质合金、工具钢、不锈钢以及某些特殊合金材料。这些材料不仅具有优异的耐磨性,能够在长期使用中保持较低的磨损率,还具备良好的耐高温性能,确保在高温环境下仍能保持稳定的机械性能和尺寸精度。此外,针对特定加工需求,如腐蚀性环境或特殊物料处理,设备表面还会进行特殊的涂层处理或热处理,以进一步提高其耐腐蚀性和使用寿命。
三、加工工艺:精密制造与质量控制
螺纹套的加工工艺涉及多道复杂工序,包括切割、磨削、热处理、表面处理等。每一道工序都需要高度的、严格的质量控制,以确保它的尺寸精度、形状精度和表面质量满足设计要求。特别是螺纹的加工,往往需要采用高精度的数控机床或专用设备,通过编程和切削参数控制,实现螺纹的成型。此外,热处理过程也是关键一环,它直接影响到设备的硬度、韧性和耐磨性。通过合理的热处理工艺,可以在保证材料强度的同时,获得较佳的综合机械性能。
四、实际应用:效率与质量的双重提升
在实际应用中,双螺杆挤出机螺纹套的性能直接影响到生产效率和产品质量。优质的设计能够优化物料流动路径,减少死角和积料现象,提高物料的均质性和塑化效果。同时,合理的剪切力分布和停留时间控制,有助于改善物料的物理性能和加工稳定性。此外,它的易维护性和可更换性也是设计时需要考虑的重要因素之一。通过模块化设计和快速更换机制,可以大大降低停机时间和维修成本,提高生产线的整体运行效率。
双螺杆挤出机螺纹套作为挤出过程中的核心部件之一,其设计、材料选择、加工工艺以及实际应用表现都直接关系到整个生产线的效率和产品质量。随着科技的进步和工业的发展,对设备的性能要求也越来越高。未来,通过不断的技术创新和优化设计,相信它将在更多领域发挥更加重要的作用。
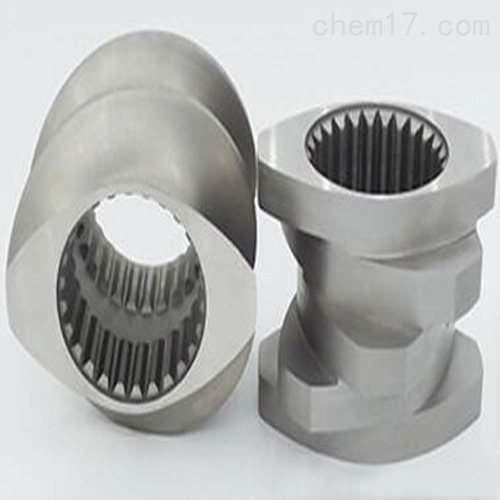